Trump Tariffs and Roofing: How It Affects the Industry
Tariffs and Roofing in the Lower Mainland: How Global Trade Influences Your Roof
The introduction of new tariffs under the Trump administration brought significant attention to cross-border trade and its impact on various industries. One such sector is roofing—a field that relies heavily on imported metals, fasteners, and other construction materials. Although tariffs might seem like an abstract economic concept, they can directly influence how roofs are built, how much projects cost, and how contractors operate in regions such as Vancouver, Surrey, and Delta. This guide examines how tariffs can affect roofing in the Lower Mainland, covering materials, market dynamics, building code requirements, budgeting tips, and transparent solutions that empower homeowners to make informed decisions.
Table of Contents
- Overview of Tariffs and Roofing
- Primary Materials Affected
- Market Dynamics in the Lower Mainland
- Statistical Insights on Roofing Challenges
- Local Building Codes and Climate Considerations
- Budgeting and Project Planning
- Alternative Approaches and Material Options
- DIY Maintenance vs. Professional Support
- Trustworthy Solutions and Next Steps
- Conclusion
1. Overview of Tariffs and Roofing
A tariff is essentially a tax placed on imported goods. When the U.S. imposes tariffs on products like steel or aluminum, suppliers shipping those materials to (or through) the U.S. face added costs. Even if a manufacturer is Canadian, it may still rely on American raw materials or cross-border distribution channels. As a result, tariffs can prompt price increases on essential roofing components, creating cost uncertainty for both contractors and homeowners.
- Scope of Impact: The roofing industry uses large quantities of metal-based parts, including flashing, fasteners, and underlay accessories that may have steel or aluminum elements. Tariff changes can alter prices for these components and drive up total project costs.
- Dependency on Cross-Border Trade: Many roofing systems in British Columbia still originate in the U.S., or require specialized equipment imported from American factories. When tariffs are introduced, shipping delays or customs bottlenecks can slow project timelines.
Although the Canadian and U.S. governments sometimes negotiate exemptions or special clauses, market jitters can still push prices upward or reduce the availability of certain roofing products. Understanding the broad strokes of how tariffs ripple through supply chains is critical in predicting their influence on roof construction and maintenance.
2. Primary Materials Affected
Steel
Steel is central to modern roofing, used in everything from standing-seam panels to the fasteners that hold shingles in place. The durability and structural benefits of steel make it indispensable, particularly when building or repairing roofs designed for heavier loads. If tariffs significantly raise steel import costs, suppliers may respond by increasing the price to local contractors.
- Metal Roofing Panels: A favored option for longevity and weather resistance, especially on commercial buildings or residential properties needing robust performance.
- Fasteners and Connectors: Steel nails, screws, washers, and clips are essential for keeping roofing structures securely attached. Even a small surcharge on these items accumulates quickly over thousands of fasteners.
- Flashing and Trim Pieces: Critical for sealing edges and preventing water intrusion, steel flashing is sometimes the most cost-effective choice. Tariffs can make these finishing materials more expensive or harder to find.
Aluminum
Aluminum is frequently used in roofing components because of its resistance to corrosion and relatively light weight. The Lower Mainland’s rainy conditions can make aluminum-based flashing and trim desirable, as aluminum weathers moisture without rusting. When aluminum is subject to tariffs:
- Gutter Systems: Aluminum gutters channel water away from rooftops and building foundations. If gutters become costlier, homeowners might be forced to select lower-grade alternatives.
- Soffit and Fascia: Aluminum often appears in soffit or fascia materials, helping air circulate in the attic and protecting roof edges from moisture.
Roofing Underlayments and Accessories
Underlayment layers, drip edges, vents, and ridge caps might also incorporate metal-based or polymer-based components subject to import duties. Although the core material might not be steel or aluminum, certain elements—like embedded metal fibers or specialized coatings—can still be affected by tariffs. Homeowners and contractors seeking consistent product performance may have to adapt to fluctuating inventory or rising costs on these secondary components.
3. Market Dynamics in the Lower Mainland
Vancouver and its surrounding communities are known for a high volume of construction and renovation projects. Local housing demand keeps the roofing industry busy, but tariffs can complicate that bustling environment.
- High Construction Activity: Continuous development means constant demand for roofing materials. Even modest tariff-driven cost surges can have a wide financial impact, affecting multiple new builds and roof replacements at once.
- Proximity to the U.S.: Being close to the Canada-U.S. border often enables quick shipping of materials from American sources. However, border tariffs can disrupt that advantage, creating sudden price shifts or availability issues.
- Brand Loyalty: Contractors who have built relationships with specific American brands may be reluctant to switch. If a favored product or supplier faces increased tariff costs, contractors might have to weigh whether to pay higher prices or transition to alternatives.
In this dynamic environment, even slight cost swings can ripple through project budgets. Contractors and homeowners who keep track of tariff developments can make more strategic choices about project timing and material selection.
4. Statistical Insights on Roofing Challenges
Roofing challenges arise from various factors, including wear and tear, design flaws, and weather-related stresses. While tariffs themselves do not cause physical damage, they can affect the feasibility and cost of preventive measures or repairs. Local meteorological data illustrates that certain times of the year see increased moisture levels, which place additional strain on roofs:
- Rainfall Frequency: The Vancouver area averages over 100 rainy days per year. The consistent dampness can slowly degrade roofing components, emphasizing the importance of high-quality materials. If tariffs push up the price of corrosion-resistant fasteners, roofs using cheaper metals may fail earlier under these conditions.
- Snow Loads: Environment Canada data indicates that Lower Mainland snowfalls can be sporadic but can still deposit heavy, wet snow on roofs. While overall snowfall accumulation is lower than in interior B.C., those occasional dumps can lead to structural challenges. If a roof is built using subpar materials due to tariff-related cost constraints, it may be more prone to stress and leaks.
- Roof Failure Rates: Official, province-wide statistics are scattered, but insurers and contractors report noticeable upticks in emergency repairs following heavy precipitation periods. An older or poorly maintained roof is particularly vulnerable if original design or replacement materials were compromised in quality or installation.
These statistics reinforce the need to secure reliable materials that can withstand the dampness and intermittent snow load typical to the region.
5. Local Building Codes and Climate Considerations
Building Codes in British Columbia
The BC Building Code sets performance standards for roofs, ensuring that structures can handle local weather conditions. Each municipality in the Lower Mainland adheres to these regulations, sometimes with localized amendments. Tariffs do not soften code requirements; every roof must still meet minimum criteria for durability, drainage, and structural integrity.
- Snow Load Calculations: Even if Vancouver’s snowfall seems modest, the code stipulates a baseline load capacity. Materials used must conform to these guidelines so that a rare heavy snowfall doesn’t compromise the roof’s integrity.
- Rainfall Management: Proper drainage and flashing are essential. When certain high-grade flashing options become costlier due to tariffs, some may consider cheaper metal. However, building codes require that flashing remain up to standard to control water infiltration.
- Ventilation and Insulation: Roofing assemblies must allow for proper air circulation to avoid moisture buildup in attics. If specialized vents or advanced synthetic underlayments get pricier, cost-driven shortcuts still cannot violate code provisions.
Climate and Cost Pressures
Because the Lower Mainland experiences high rainfall, routine maintenance is already crucial. Tariffs can exacerbate budget constraints, potentially discouraging homeowners from investing in the best possible roofing solution. The risk is that short-term savings might lead to long-term expenses if subpar materials fail prematurely in Vancouver’s damp environment.
6. Budgeting and Project Planning
Early Research
Property owners looking to replace or repair a roof can minimize tariff surprises by consulting multiple suppliers. Material pricing can vary significantly, even within a single metro area. Understanding each product’s origin—domestic vs. international—helps in recognizing which items might be more exposed to import costs.
Detailed Quotes
Roofing contracts sometimes include an escalation clause for materials. If tariffs escalate mid-project, contractors might pass added costs to clients. Clarifying these details upfront avoids misunderstandings. It’s prudent to compare quotes from two or three companies, asking each one how they handle potential material cost fluctuations.
Timing
Homeowners with flexibility may choose to schedule large roofing projects in periods when costs are stable. Tariff-related spikes sometimes occur after major announcements or enforcement changes. Monitoring trade news or discussing timing with suppliers can uncover optimal windows for purchasing materials. In some cases, local promotions or bulk-purchase deals can partially counteract tariff-driven increases.
Contingency Funds
Setting aside a contingency of about 10–15% above the quoted roofing budget can alleviate the shock of sudden cost changes. If local supply issues or cross-border fees push material prices higher, a built-in financial cushion reduces stress. Should the project finish under budget, that excess can always be reallocated to other home improvements.
7. Alternative Approaches and Material Options
Locally Manufactured Products
One way to sidestep tariff uncertainty is by choosing materials produced entirely within Canada. Some regional manufacturers or distributors either source raw materials domestically or maintain less reliance on U.S. imports. While these options might still be susceptible to global market forces, they may be better insulated against specific U.S.-imposed tariffs.
Composite or Asphalt Shingles
Asphalt shingles often remain a mainstay in residential roofing. Although certain additives or reinforcements might come from the U.S., many asphalt shingle products are made in Canada. For property owners feeling the pinch of tariff-driven metal roofing costs, high-grade asphalt shingles can be an alternative that balances budget and durability.
Metal Blends and Coatings
If the goal is a metal roof, exploring different metal blends or coatings can help. Some steel roofing panels are coated with specialty compounds that originate locally, making them less prone to tariff fees. Another approach is using materials with a higher post-consumer recycled content—sometimes these products have separate trade classifications that may escape certain tariffs.
Upgrade Priorities
If a roof upgrade includes multiple high-end elements (for instance, specialized venting, ultra-durable coatings, or ornamental metal accents), focusing on one feature at a time can sometimes manage budget flow. If certain ornamental or aesthetic metalwork has soared in price, saving it for a future phase may allow you to lock in the essential structural elements first.
8. DIY Maintenance vs. Professional Support
Routine Upkeep at Minimal Cost
Regular rooftop maintenance is one of the best ways to mitigate tariff-related expenses. Some simple do-it-yourself tasks help extend a roof’s lifespan:
- Clearing Debris: Leaves or branches can collect in roof valleys or gutters, leading to moisture retention. Regular clean-ups reduce corrosion risk, allowing you to postpone more costly interventions.
- Visual Inspections: Observing shingle wear, rust spots on flashing, or loose fasteners can catch problems early. Replacing a handful of screws is less expensive than an entire re-deck if water damage sets in.
When to Hire a Professional
For significant repairs, structural assessments, or roof replacements, professional expertise ensures that building codes are met and that safety risks are minimized. Tariffs may influence the price of materials, but they do not reduce the need for a properly installed system:
- Complex Roofs: Multi-sloped designs, skylights, and dormers require specialized methods. A professional ensures that each area receives the correct underlayment and flashing types.
- Code Compliance: An experienced roofer remains updated on local regulations. This knowledge is vital when certain materials become expensive or scarce. Substitutions must still satisfy code standards.
- Liability and Insurance: Working on roofs can be risky. Professional contractors typically carry insurance and warranties that protect clients if something goes wrong. This coverage can be particularly important when dealing with high-end metal roofs.
9. Trustworthy Solutions and Next Steps
Transparent Communication
Reputable roofing companies outline how tariffs affect the availability and cost of materials. Good contractors provide itemized estimates and present alternative product lines when fees soar. Open dialogue reduces unwelcome surprises and fosters a cooperative approach to problem-solving.
Sourcing Strategies
Some roofers negotiate bulk deals or hold extra inventory to buffer against sudden import cost spikes. Others pivot to Canadian or overseas manufacturers not impacted by U.S. tariffs. Clients benefit from these efforts because it may stabilize pricing or enable quicker turnarounds.
Balancing Quality and Budget
Although tariffs might encourage selecting cheaper materials, it is important to consider long-term costs. A low-grade metal or underlayment that fails prematurely can lead to higher cumulative expenses over the roof’s lifecycle. Balancing immediate affordability with projected longevity can often save money down the line.
Monitoring Policy Changes
Trade policies can shift after elections or new negotiations. Staying informed about these developments helps in planning upcoming roofing projects. When tariffs ease, local suppliers might reduce prices or expand product lines. Conversely, if tariffs intensify, proactive measures can be taken to purchase materials before costs climb further.
10. Conclusion
Tariffs imposed by the Trump administration—and any subsequent adjustments—have a tangible impact on the roofing industry. They can shape the price and availability of steel, aluminum, and other critical components used in both residential and commercial roofing systems. In a region like the Lower Mainland, where climate conditions demand reliable, well-maintained roofs, homeowners and contractors must stay alert to these economic changes.
Although tariffs can complicate planning, there are effective strategies to manage the resulting challenges. Comparing locally sourced materials, exploring alternative product lines, staying current on policy updates, and maintaining open communication with suppliers or roofing professionals all help mitigate risks. Robust building codes in British Columbia remain a critical backstop; no matter how market conditions shift, roofs in the region must still protect buildings from rainfall and occasional snow loads.
A well-informed homeowner or property manager is more likely to navigate tariff-related cost fluctuations without compromising on essential quality. By understanding how tariffs enter the roofing supply chain, planning for budget shifts, and adhering to local code requirements, roofing investments can remain secure. Taking proactive steps—whether via routine maintenance or comprehensive project scheduling—further shields homeowners from unwelcome surprises and fosters roofs designed to last, regardless of global trade uncertainties.
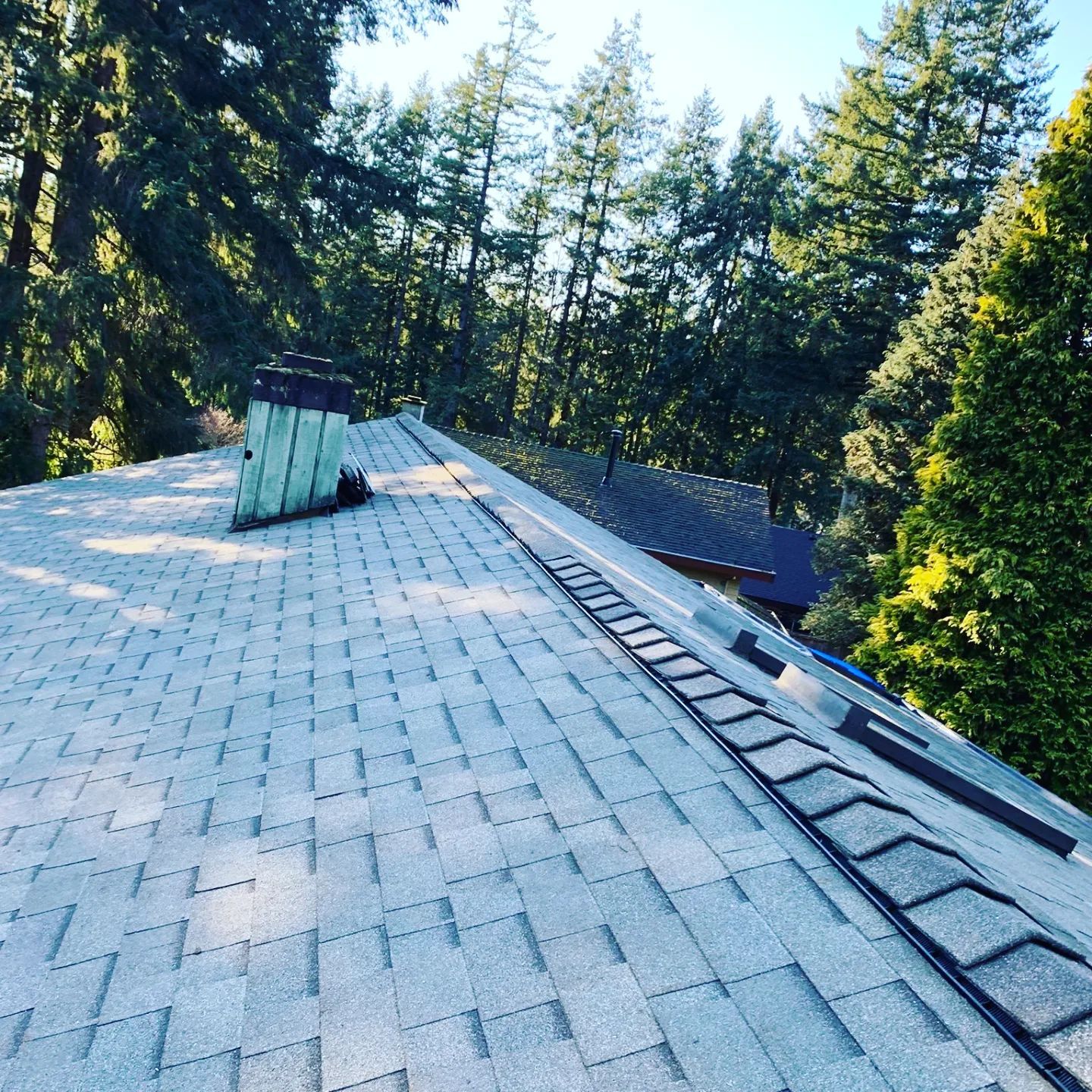
Our Roofing Blog
Have more questions about roofing?
Check out our FAQs or give us a call today to speak to an expert roofer in Vancouver Lower Mainland, BC. We're here to help our neighbours make educated decisions about their roof. For our team, we value helping clients save money while making their roofs last.